مقره با لایه گرافیتی
مقره سوزنی است که روی سر آن تا سطح مشخص از قشر سیاه گرافیت پوشیده شده است که این قشر میدان الکتریکیرا بطور یکنواخت در سطح مقره توزیع نموده و از تمرکز آن در نزدیکی محل اتصال هادی به مقره ممانعت می نماید. بدین ترتیب با جلوگیری از تخلیه جزیی اولا تولید پارازیت ها مزاحم فرکانسهای رادیویی منتفی شده و ثانیا خورده شدن سطح مقره به وقوع نمی پیوندد.این مقره در مناطقی که خطوط در ایستگاه های مخابراتی و رادیو وتلویزیون مستقر می باشند مورد استفاده قرار می گیرند.
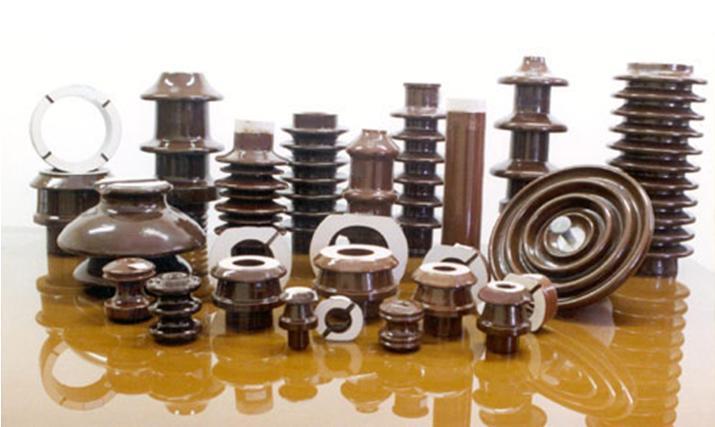
مقره بشقابی
مقره بشقابی
این نوع مقره در خطوط انتقال فشار قوی و فوق توزیع و ولتاژ متوسط بکار می روند. در خطوط ولتاژ متوسط در مواردی که بهر علتی نیروی استقامت مکانیکی مقره باید بالاتر از حد نرمال و متعارف باشد (در پایه های کششی ،انتهایی ، زاویه ای،اسپنهای بزرگ، استفاده از سیم های سنگین) این نوع مقره مورد استفاده واقع می شود. این مقره ها از کراس آرم آویزان شده یا در امتداد هادی قرار میگیرند. از مزایای این نوع مقره ها این است که چنانچه مقره دچار شکست الکتریکی شود اجزای چینی سیم را رها نمی کنند و سیم هادی به زمین نمی افتد. بدین جهت در اسپنهای عبوری از جاده ها و نقاط حساس توصیه میشود که از این نوع مقره ها استفاده میشود.
مقره اتکایی
مقره ای اتکایی
این نوع مقره ا بصورت عمودی یا افقی نصب میگردند و نیاز به کراس آرم ندارند.آنها بشکل استوانه چینی تو ر یا تو خالی ساخته میشوند.نوع توخالی آن به شکل استوانه ای است که در یک انتهایش یک حفره دارد که قبل از اینکه قاعده مقره به کلاهک فلزی چسبانده شود پوشانده میگردد. باید دانست که مقاومت مکانیکی مقره های اتکایی تو پر در اثر افزایش قطر کاهش می یابد لذا برای تحمل نیروهای مکانیکی بزرگ نمی توان از این نوع مقره استفاده کرد، بنابراین استفاده از مقره های تو خالی معمولتر می باشد.این مقره ها معمولا در محلهایی که به فاصله خزشی زیاد نیاز می باشد استفاده میگردد. کاربرد این مقره هم اکنون در شبکه توزیع بسیار محدود می باشد.
مقره چرخی
مقره چرخی یا قرقره ای
این مقره ها در خطوط توزیع فشار ضعیف هوایی کاربرد دارد و جهت عبور سیم مورد استفاده قرار میگیرد.
مقره مهار
مقره مهار
این مقره ها در مسیر سیمهای پایه های خطوط مورداستفاده قرار میگیرند و قسمت پایین سیم مهار را از قسمت بالایی آن عایق می کنند تا ایمنی جان افراد ر پایه مهار به خطر نیفتد. همچنین با عایق نمودن قسمت بالایی سیم مهار از زمین ایمنی جان سیمبان را در هنگام کار روی تیر تامین می نمایند این مقره ها بگونه ای طراحی و ساخته میشوند که در صورت شکست ، سیم مهار رها نمیگردد و بر روی زمین نمی افتد.
سیلیکون رابر کششی
مقره سیلیکون رابر کششی
در نگاه اول در شکل ظاهری مقره های ساخته شده توسط سازندگان مختلف بجز رنگ آنها تفاوت کلی دیده نمی شود ولی با کمی دقت در جزییات ی توان به تفا وت های اساسی پی بردکه اگرچه ممکن است ناچیز به نظر برسد ولی در عملکرد و عمر مقره تاثیر قابل توجه و تعیین کننده ای دارد، از موارد بسیار مهم این تفاوت می توان به ضخامت لاستیک سیلیکونی در بشقابها در قسمت متصل به میله و لبه ها اشاره نمود . به عنوان نمونه می توان به 2 مقره اشاره نمود که یکی با ضخامت های کم و یکی با ضخامت دو برابر آن تولید شده است بفرض مرغوبیت مواد خام و کیفیت یکسان در ساخت قیمت تمام شده مقره نخست حدود 30 درصد ارزانتر از مقره دومی خواهد بود در حالیکه عمر مفید آن حدود نصف مقره نخست برآورد می گردد.توضیح اینکه حداقل ضخامت پوشش میله باید 4 میلیمتر باشد و ضخامت پره ها در قسمت اتصال به میله در حدود 8 میلیمتر و در لبه ها حدود 2.5 میلیمتر باشد. حال چنانچه به همراه کمتر بودن ضخامتها مواد با کیفیت نازلتر نیز بکار رفته و روش ساخت هم ضعیف تر باشد به همان نسبت اثر آن در ارزان شدن قیمت مقره و البته در عمر مقره بیشتر خواهد بود.
در حال حاضر مقره های کمپوزیتی خطوط انتقال نیرو با طرح هایی به شرح ذیل ساخته می شوند :
1- به شکل میله ای باطرح یکپارچه به روش تزریق یکپارچه
2- شکل میله ای با طرح یک پارچه به روش پرس قالبی
3- به شکل میله ای با طرح مدولاریا
4- مقره های مرکب (به شکل کراس آرم) که با استفاده از یکی از روشهای بالا ساخته می شود.
الف : تولید به روش تزریق یکپارچه تحت فشار و حرارت زیاد.
مقره هایی که به روش تزریق یکپارچه ساخته می شوند دارای مزایایی به شرح زیرند:
1- بدون درز هستند و درنتیجه نیازی به آببندی در مفصل مشترک بین میله و بشقاب میله و فیتینگ ندارند چون سیلیکون رابر تزریق شده در قالب قسمتی از لبه های بیرونی دهانه فیتینگ را نیز دربر می گیرند.
2- در دراز مدت و تحت استرس های کاری عملکرد بهتری دارند.
3- زمان تولید هر مقره در مقایسه با دو روش دیگر به مراتب کوتاه تر بوده و در نتیجه نیروی کاری کمتری صرف میشود.
ب: تولید به روش پرس قالبی
از مزایای تولید به این روش میتوان به موارد زیر اشاره کرد :
1- هزینه تولید نسبت به روش تزریق یکپارچه کمتر است
2- هدر رفتن مواد کمتر است
3- ظاهر مقره مانند مقره های ساخته شده به روش تزریق یکپارچه است .
از معایب تولید به این روش به موارد زیر میتوان اشاره کرد:
1- احتمال باقی ماندن حباب هوا در قسمت هایی از مقره
2- باقی ماندن قسمتی از میله در معرض هوا در فصل مشترک محل ورود میله و دهانه فتینگ که باید آنرا با چسب یا ژل سیلیکونی RTV آب بندی نمود تا از قرار گرفتن آن قسمت از میله در معرض هوا و رطوبت های اسیدی جلوگیری گردد.
ج : تولید به روش مدولار
1- تنظیم آسانتر اندازه ها
2- هدر رفتن کمتر مواد
3- نبود خط قالب در طول میله
تقریبا در اقلب گزارشهایی که پس از انجام مطالعات در مورد نحوه عملکرد مقره های کامپوزیتی و دلایل بروز عیب های مکانیکی در آنها منتشر گردیده علت کامل نبودن آب بندی آن قسمت در هنگام ساخت و یا از بین رفتن مواد آب بندی به مرور زمان براثر عوامل مختلف ذکر شده است که از آن جمله می توان به اشعه ماورائ بنفش حاصل از تابش خورشید و وجود کرونا در اطراف میله و بشقاب مقره در طرف متصل به هادی در اثر تولید شدن اوزون اشاره نمود که شایع ترین موارد در این نوع مقره ها می باشد.
معایب تولید مدولار
1- بجای خط قالب در امتداد میله درز بین محل قرار گرفتن بشقاب ها در روی میله وجود دارد که لازم است با چسب سیلیکونی RTV اب بندی شود در صورت کامل نبودن این آب بندی و باقی ماندن مجرای سوزنی در بین سطح میله و جدار سوراخ بشقاب از فاصله خزشی جریان نشتی مقره حذف میگردد.
2- باقی ماندن فاصله (گپ) و قرار داشتن قسمتی از میله در معرض هوا مانند روش تولید پرس قالبی
3- دیگر اینکه در دراز مدت احتمال ایجاد ترک های شعاعی بر اثر استرس حلقوی وارد شده به جدار سوراخ بشقاب ها وجود دارد که به تدریج توسعه یافته و موجب بروز کرونا و تشدید در فساد تدریجی روکش میله در آن قسمت گردیده و در نهایت به سطح میله فایبر گلاس می رسد.و میله در معرض هوا و رطوبت های اسیدی قرار میگیرد و در اثر خوردگی تدریجا استحکام مکانیکی خود را از دست میدهد بطوری که پس از مدتی بسته بشدت خوردگی ممکن است گسیختگی اتفاق بیفتد.
سیلیکون رابر
امروزه سیلیکون رابر مرغوب قابل استفاده در صنعت توسط چند سازنده معتبر تولیدمی شود. تولید کنندگان کمپوند خود برای تولیداتشان مسخصاتی تایین کرده اند و اطلاعات مربوط را در صورت تقاضای مشتریان در اختیار آنها قرار می دهند همچنین سازندگان مقره ترجیح می دهند با فورمولاسیون تجربه شده و مورد قبول خودشان را به تولید کنندگان سفارش دهند و طبق قوانین این فورمولاسیون انحصاری بوده و تولید کننده کمپوند نمی توند بدون اجازه مالک کمپوند مذکور را به دیگران بفروشد.
مواد تشکیل دهنده سیلیکون رابر عبارتند از :
1- سیلیکون
2- فیلر
3- روغن سیلیکون
4- افزودنی های دیگر
هر یک از مواد بالا نیز انواع مختلفی دارند که در نوع و کیفیت کمپوند موثر است.
نظرات شما عزیزان: